In military aerospace applications, engineers are constantly challenged to do more in a smaller package, including circuits for critical systems and external payloads. The main driving force for new interconnects lies in SWaP connectors that support compact, rugged, and lightweight circuit designs while supporting a mixed variety of signal and power levels. But what is SWaP, and why is it important?
What is SWaP?
The acronym SWaP stands for Size, Weight, and Power and was originally an initiative employed by the US military and NASA. SWaP has helped connector manufacturers maintain a focus on developing connectors that are both smaller and lighter. Some may incorrectly assume that any Mil-Spec connector would be suitable. Still, traditional Mil-Spec connectors (i.e., MIL-DTL-38999 connectors) contribute to the weight burden of designs because they are relatively large, heavy, and not suited for applications such as embedded high-speed systems.
Benefits of SWaP-Optimized Connectors
Electronics engineers, in general, are pushing for smaller, lighter interconnects for a variety of reasons, including the need to meet tight space constraints. SWaP connectors allow engineers to shrink the existing footprint without decreasing functionality and to simplify board layouts. SWaP connectors also contribute to increased quality assurance and reduced costs. These connectors make it possible to create shorter, more direct interconnections that allow for faster signals and response times. And because they are small connectors, vibration is reduced, leading to greater stability.
SWaP Connectors and Military Aerospace Applications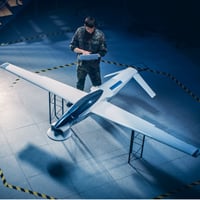
Soldier-worn equipment and UAVs (Unmanned Aerial Vehicles) have both significantly advanced over the last few decades, including reduced processor and memory sizes. Soldiers are now carrying computer processing power on their bodies that once would have filled a room. These advancements require less voltage and current, resulting in smaller wires, and therefore smaller connectors. Utilizing connectors with both power and signal/data contacts reduces the number of cables and connectors that go into the electronic module.
Size, weight, and power density remain critical, as well as the ability to transmit power, data, and signals. Lighter SWaP connectors can decrease the weight burden for soldiers carrying equipment on their bodies, allowing for greater mobility and endurance. Keep in mind that devices such as batteries, GPS, tablets, weapon optics, and night vision add up to around 20 pounds for a soldier to carry. Weight can also be particularly essential when designing UAVs because they must support additional payloads that can include cameras (e.g., visual and thermal) and LiDAR (Light Detection and Ranging) in addition to integral power, guidance, and control systems. Both soldier-worn equipment and UAVs are also subject to vibration, impact, and shock loadings that can dislodge a poorly specified connector.
Cinch Dura-Con Micro-D M83513 Connectors 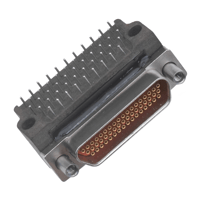
The Cinch Dura-Con Micro-D M83513 connector series is an excellent SWaP connector solution for UAVs. These Mil-Spec Micro-D connectors are rugged, robust, and reliable. Their reliability is achieved using a wire form pin with twist pin technology that provides seven points of contact when mated. They also offer high-performance levels and can inter-operate/inter-mate with other connectors installed in a UAV.
Additionally, all rectangular microminiature D-Sub connectors with solder or non-removable crimp contacts used in military applications UAVs (drones) must comply with the MIL-DTL-83513 specification. This specification is provided by the USA’s Defense Logistics Agency (DLA), which covers connectors that are suitable due to their weight and size.
These lightweight Cinch microminiature D-Sub interconnects are designed to MIL-DTL-83513 standards for reliability and meet MIL-STD-1344 requirements. They have a current rating of 3A and a wide operating temperature range of -55°C and 125°C. Cinch Dura-Con Micro-D M83513 connectors can also withstand shock loadings of 50 Gs (per MIL-STD-1344, Method 2004, Condition E) and 20 Gs of vibration (20 G’s per MIL-STD-1344, Method 2005, Condition IV), making them ideal for the rugged conditions faced by UAVs.
PEI-Genesis: SWaP-Optimized Solutions for Your Designs
Whether they are being used for soldier-worn GPS systems, the guidance system on a UAV, or external LiDAR, SWaP-optimized connectors provide many features beneficial for various military applications. For aerospace designs in need of rugged, reliable, SWaP optimized connectors, let the experts at PEI-Genesis help. Our team of connector experts and engineers can aid you in specifying the suitable space and weight-sensitive Mil-Spec interconnect solution for your application.